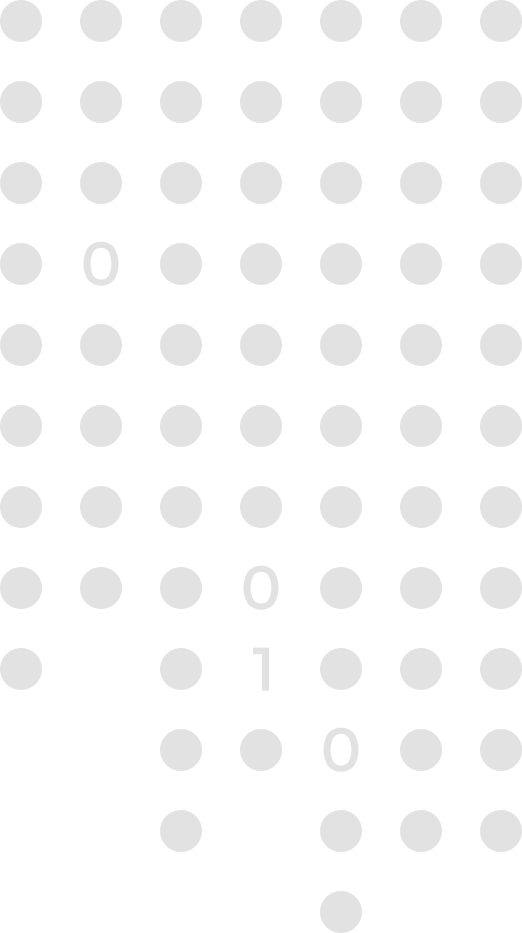
Use Cases –
the Digital Twin in practice
How does the Digital Twin work in industrial practice? Concrete examples from component manufacturers, machine and plant builders and operators show approaches to solutions and resulting benefits.
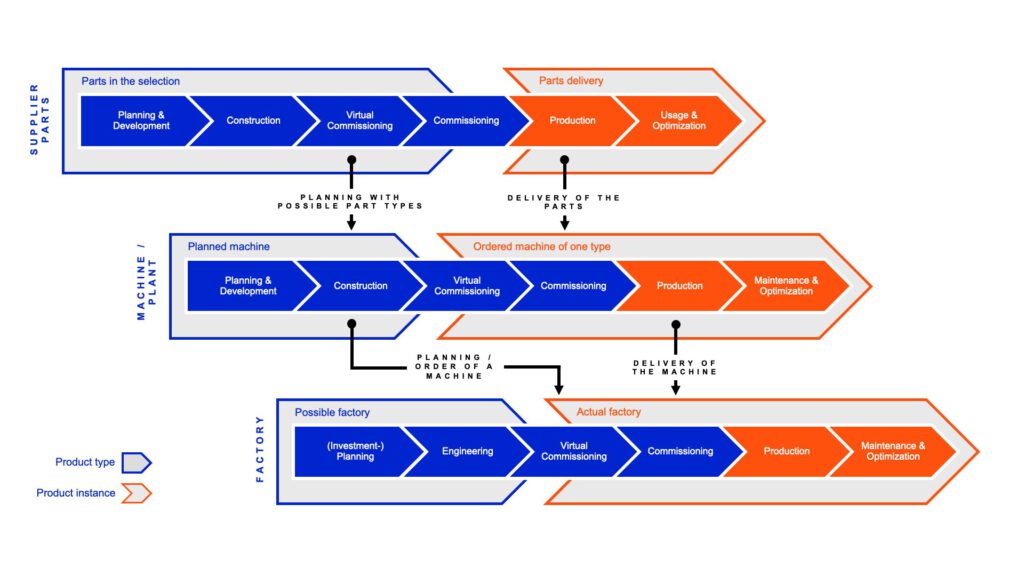
Our use cases show concrete applications of the Digital Twin along the industrial life cycle, from the perspective of component manufacturers, machine and plant builders and operators, according to IEC 62890.
Choose from the use cases according to the role of the value-added partner and a lifecycle phase.
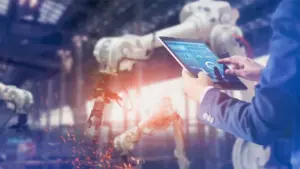
Installation of an AAS-based system in two pilot plants as reference model.
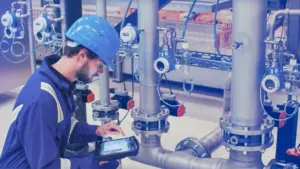
Remote commissioning of plants, (semi)automatic onboarding and initialisation of a Digital Twin in the Asset Management System.
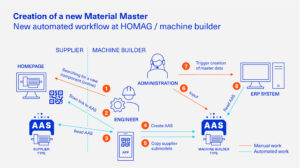
The material master for new components is created by direct transfer from the respective Asset Administration Shell instead of by manually entering values.
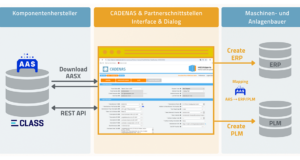
Automated master data creation with ENTERPRISE 3Dfindit and the AAS Industry Data Standard saves resources, increases efficiency and improves data quality.
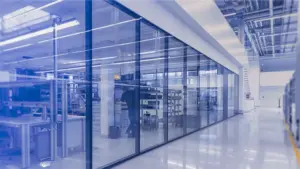
In the AI Real Lab at the SmartFactoryOWL in Lemgo, the discovery and secure sharing of data in multilateral corporate structures is being tested based on Gaia-X Federation Services and management shells.
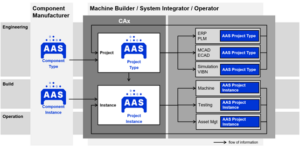
The Digital Twin of a machine is created in the software systems (ECAD, MCAD, etc.) of all companies involved in the process using digital and physical components from countless manufacturers.
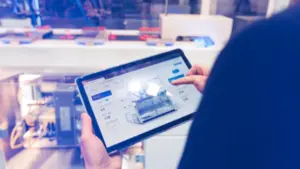
It contains all product information in digital form, provides extended product services, can be updated at any time and dispenses with paper resources.
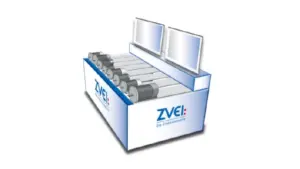
Cooperation between manufacturers of electric drives: For the first time, the interoperability of electric drives is demonstrated in a practical application using the management shell.
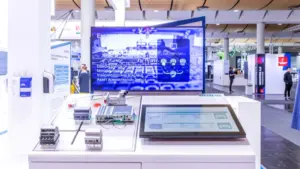
Standardised submodels provide transparency about the energy consumption of a production at any time and enable the quick replacement of a device, without engineering effort.
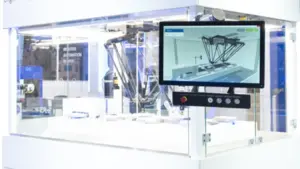
Automatic, updateable integration of all content relating to machine components and assemblies in an asset management solution from the development phase of a machine.
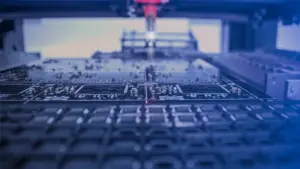
The Asset Administration Shell provides all relevant data of sensors over the entire life cycle in standardized formats in a machine-readable format.
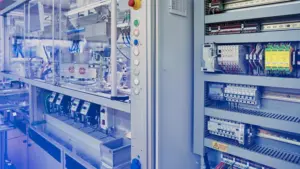
Calculation of the Product Carbon Footprint (PCF) of own and purchased products along the entire value chain.
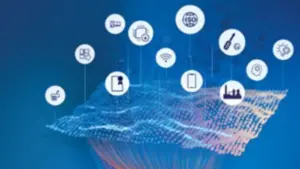
Implementation of the digital nameplate based on the Asset Administration Shell and nameplates in accordance with DIN SPEC 91406.
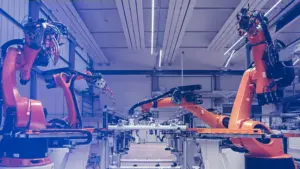
Seamless flow of information from supplier to customer and vice versa, for more efficiency in the value chain.
Message
Write us!
Do you have questions about the Digital Twin or the Asset Administration Shell? Please feel free to contact us! Together we will see how the Digital Twin can be used in your company. We look forward to the exchange!