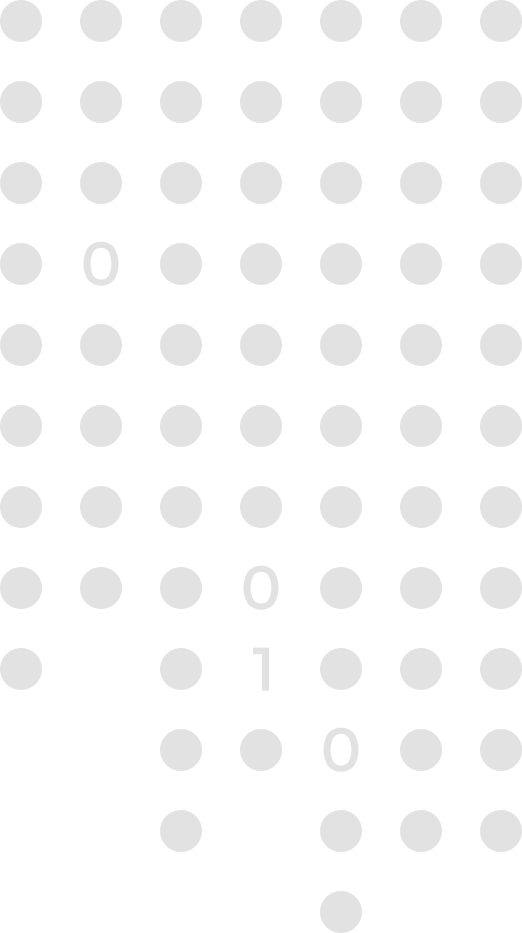
IDTA welcomes Mitsubishi Electric as its 100th member
The association for the implementation and design of the industrial Digital Twin is continuously growing
Mitsubishi Electric Europe has joined the Industrial Digital Twin Association e.V. (IDTA) and is the 100th member in the alliance for the joint establishment and development of the standardised Digital Twin for industry. Since its founding in September 2020 with 23 constituent members, 100 companies from the electrical and digital industries, mechanical engineering, the software industry and end users have come together up to the present day to implement the Digital Twin based on the Asset Administration Shell (AAS). Member companies benefit from the transparent exchange of knowledge in the network along the value chain and early active participation in the technology. Mitsubishi Electric Europe, as a manufacturer of electrical and electronic equipment applied in industrial technology, information processing, transport and numerous other areas, has been following the development of the AAS from the beginning and will contribute experience to the IDTA network in the future.
“The openness, high flexibility and manufacturer independence are decisive building blocks for the digitisation of the industry. Various functionalities for data exchange are already integrated in our own products. Through numerous exemplary implementations and projects related to Industry 4.0, we have good experience with the AAS. We now want to bring this experience into the IDTA and, for the benefit of our customers, drive forward the further development and standardisation in the IDTA with other members. We are particularly honoured to do this as the hundredth member,” says Andreas Pfaff, Division Manager of the Factory Automation European Development Center at Mitsubishi Electric.
The aim of the IDTA is to establish the Digital Twin for components, machines, plants and entire factories as an open-source technology and to develop it further together with industry. Thanks to open standards, the AAS facilitates the exchange of information across different manufacturers. Coordination between development, production and application is improved. Redundant and inconsistent information management decreases. This reduces effort, integration time and costs throughout the entire value chain. In addition to productivity, efficiency and transparency, the AAS also makes a valuable contribution to the environment and climate protection as well as to the future circular economy. This is associated with potential for new business models for small and medium-sized factory equipment suppliers as well as for larger end users.
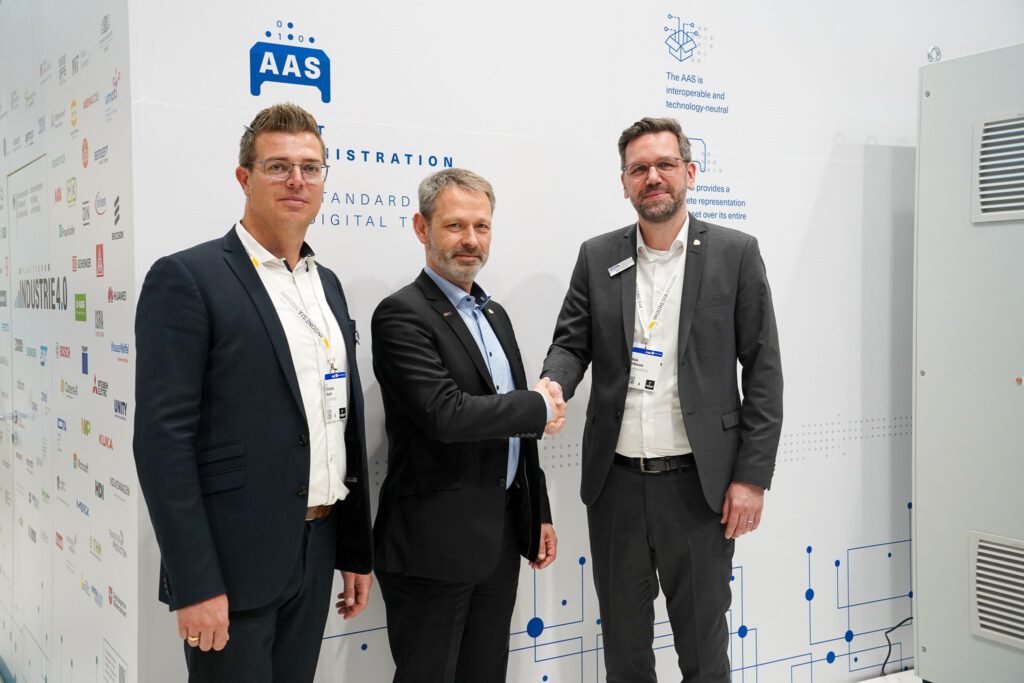